In industrial and mechanical systems, the concept of load sharing plays a vital role in ensuring the smooth operation of processes that require multiple motors to drive a single load. By enabling each motor to contribute its fair share of power, load sharing not only ensures efficient energy usage but also prevents undue strain on any single motor. This article can give you a basic understanding of load sharing in AC drive applications, exploring the conditions where it is necessary and the control strategies used to achieve it.
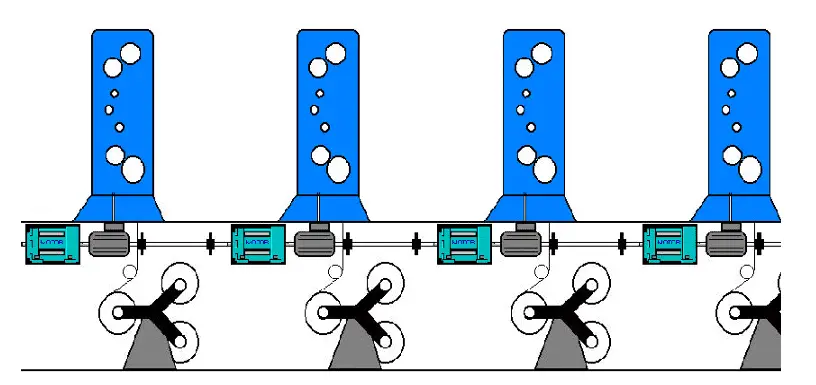
Understanding Load Sharing
At its core, load sharing involves multiple motor and drive combinations working in harmony to power a common mechanical load. The primary goal is to ensure that the torque generated by each motor is proportional to its capacity, thereby avoiding overloading or underutilizing any single motor. It is crucial to distinguish load sharing from simply running multiple motors on a single drive. The latter does not allow for individual torque control and, therefore, does not meet the criteria for load sharing.
Applications that benefit from load sharing typically involve high-power or critical operations where precise control over torque distribution is essential. Examples include conveyors with synchronized rolls, large industrial kilns, and other processes where seamless cooperation between motors is a necessity.
Key Control Strategies for Load Sharing
Effective load sharing relies on sophisticated control techniques that enable precise coordination among multiple drives and motors. These techniques fall into three primary categories:
- Droop Control
- Torque Follower Control
- Speed Trim Follower Control
Let’s examine each in detail.
1. Droop Control
Droop control is the simplest method of implementing load sharing. This approach works by reducing the output frequency of a drive in proportion to the load current, thereby leveraging the natural slip of the motor to balance the load. While this method is straightforward to configure, it has limitations in terms of precision and flexibility. The accuracy of droop control depends heavily on the motor’s characteristics, the drive’s control algorithm, and the type of load being driven.
Droop control is best suited for applications where exact speed regulation is not a priority, such as:
- Air handling systems with a common discharge.
- Continuous belt conveyors with multiple driven rolls.
Although it lacks the precision of more advanced methods, its simplicity makes it an attractive option for less demanding scenarios.
2. Torque Follower Control
Torque Follower control offers a higher level of precision by utilizing drives capable of operating in “torque mode.” In this setup, one drive, known as the Master, operates in “speed mode,” while the other drives, referred to as Slaves or Torque Followers, operate in “torque mode.”
The Master drive generates a torque command, which is distributed to the Slave drives, ensuring that each motor contributes appropriately to the load. This method is particularly effective in applications requiring precise torque sharing, such as:
- Large-diameter bull gears.
- Printing presses with inline drive shafts.
- Coal car dumpers.
By providing direct control over the torque contribution of each motor, this method minimizes the risk of imbalances and enhances system reliability.
3. Speed Trim Follower Control
Speed Trim Follower control combines elements of speed regulation and torque adjustment to achieve continuous load sharing. In this configuration, both the Master and Follower drives operate in speed regulation mode and receive a common speed reference. The torque reference from the Master drive is shared with the Follower drives, enabling them to adjust their output to match the Master’s torque.
This method provides automatic compensation for load variations and is ideal for applications prone to oscillations or requiring fine-tuned control, such as:
- Cement kilns.
- Separator drums.
The continuous adjustment capability of Speed Trim Follower control ensures optimal performance even in dynamic operating conditions.
Load sharing in AC drive applications is indispensable for industries where multiple motors must work together to drive a single load. By understanding the principles of load sharing and implementing the appropriate control techniques—whether it be Droop, Torque Follower, or Speed Trim Follower—engineers can achieve balanced torque distribution, enhanced efficiency, and reliable system performance.
For each application, the choice of control strategy will depend on the precision requirements, the nature of the load, and the system’s operational dynamics. With careful planning and the right approach, load sharing can unlock significant operational benefits, ensuring longevity and efficiency in critical industrial processes.
Here is a great resource: https://open.library.ubc.ca/media/stream/pdf/24/1.0072455/1